Multi-head tubular machines represent a transformative advancement in manufacturing processes, offering a substantial acceleration of turnaround times for custom orders across various industries. The integration of these sophisticated machines into production workflows introduces a range of features and capabilities that collectively contribute to enhanced efficiency and responsiveness.
One of the key advantages lies in the simultaneous processing capability of multi-head tubular machines. Unlike traditional single-head machines, these advanced systems can execute multiple operations concurrently. This simultaneous approach expedites the manufacturing process by addressing different facets of a custom order simultaneously, eliminating the need for sequential operations and significantly reducing the overall production time.
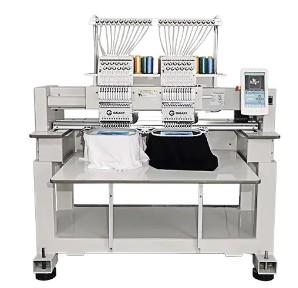
Additionally, the batch processing capabilities of multi-head machines further contribute to efficiency. By accommodating the simultaneous production of multiple components or products within a single setup, manufacturers can optimize their processes for economies of scale. This proves particularly advantageous for custom orders that involve the production of several identical or similar items, allowing for streamlined and accelerated manufacturing.
High throughput is a defining characteristic of multi-head tubular machines. The utilization of multiple heads enables these machines to achieve a higher overall production capacity. With each head capable of independent or collaborative work on distinct aspects of a custom order, the aggregate throughput is substantially increased. This elevated production capacity becomes instrumental in meeting the demands of custom orders with tight deadlines.
The versatility of tooling is another pivotal aspect that contributes to the efficiency of multi-head machines. Equipped with a variety of tools and attachments, these machines can adapt swiftly to different manufacturing requirements. This adaptability allows manufacturers to produce complex and customized designs without the need for manual intervention or extensive machine reconfiguration, further streamlining the manufacturing process.
Changeover time, a critical factor in turnaround time, is significantly reduced with multi-head tubular machines. Quick tool changes, automated adjustments, and efficient calibration processes enable manufacturers to transition seamlessly between different custom orders. The minimized changeover time reduces downtime, ensuring that the machines are operational and productive for a larger proportion of the overall manufacturing process.
Precision and accuracy are inherent in the design of multi-head tubular machines. These machines can maintain tight tolerances across multiple dimensions, ensuring that each component or product meets the specified design requirements. The reliability of precision in production contributes to a reduction in the need for rework, ensuring that custom orders are completed with a high degree of accuracy and efficiency.
Moreover, the integration of multi-head tubular machines with digital technologies enhances the overall efficiency of the production process. These machines seamlessly interface with CAD/CAM systems, facilitating rapid data transfer, automated toolpath generation, and improved communication between design and manufacturing teams. The digital integration not only expedites the programming and adjustment processes but also ensures a more seamless transition from design to production.